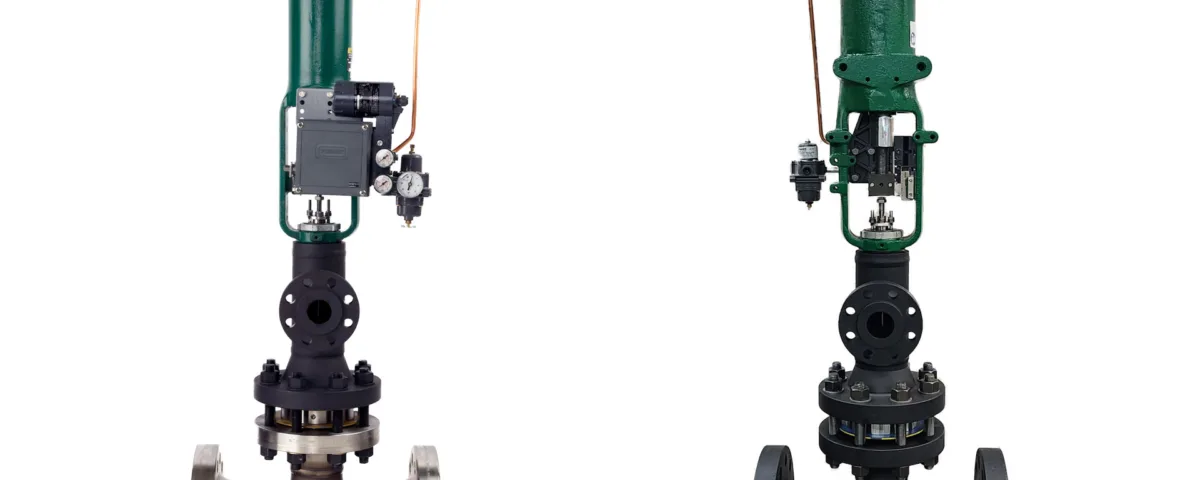
The Challenge
An electricity-generating power plant has high-pressure steam (600 psi) and was looking to heat the incoming boiler feed water to feed through reverse osmosis (RO) membranes in an effort to reduce the use of chemicals in their boilers. By filtering the water through RO systems, this can be achieved while keeping their boiler optimized and maintaining higher “green” standards, part of their corporate and city goals. The problem is that their high-pressure steam and high temperatures are tough on a lot of industry-standard water heating equipment. Space in the boiler room area was also limited, adding to their challenge.
Key Requirements
- Heat the incoming water in the colder months to 70°F to optimize the RO filtering process.
- Reliability to enable the boiler to run 24/7/365.
- Maintain green standards to meet corporate, city, and county goals.
- Utilize equipment that can stand up to the pressures and temperatures of 600 psi steam.
- Meet the small footprint space available to add equipment.
Solution
ProSonix worked with the customer to fully understand their requirements, review the steam pressure and temperatures, and discuss proper piping and valve requirements. ProSonix then provided a solution of the PSX I-Series inline heater with our Patented special high-pressure seals, gaskets, and pressure ratings to meet their requirements. The ProSonix I-Series is a reliable, cost-effective, energy-efficient heater with a very small footprint that promises easy installation and maximum total uptime. All heaters are built in the USA in Milwaukee, WI, and ensure the customer has the hot water they need when they need it and at an accurate temperature for optimum performance of the RO system.
Summary
The ProSonix I-Series heater provided the following benefits:
- Met the high-pressure steam and temperature requirements to ensure trouble-free performance with reliability and total uptime – getting them the hot water they needed, when they needed it.
- Helped the customer meet their green initiatives by ensuring the RO system was optimized, reducing chemical requirements in the boiler, and also proving to be 99% energy-efficient in the heating process.
- Due to the I-Series’ simple inline installation, the heater was installed directly in the piping, which required almost no footprint space and also made it easy to do any preventative maintenance on it.
Learn more about our High-Pressure PSX I-series heaters here.